Resources
The technology principles of the release film
2025/04/30
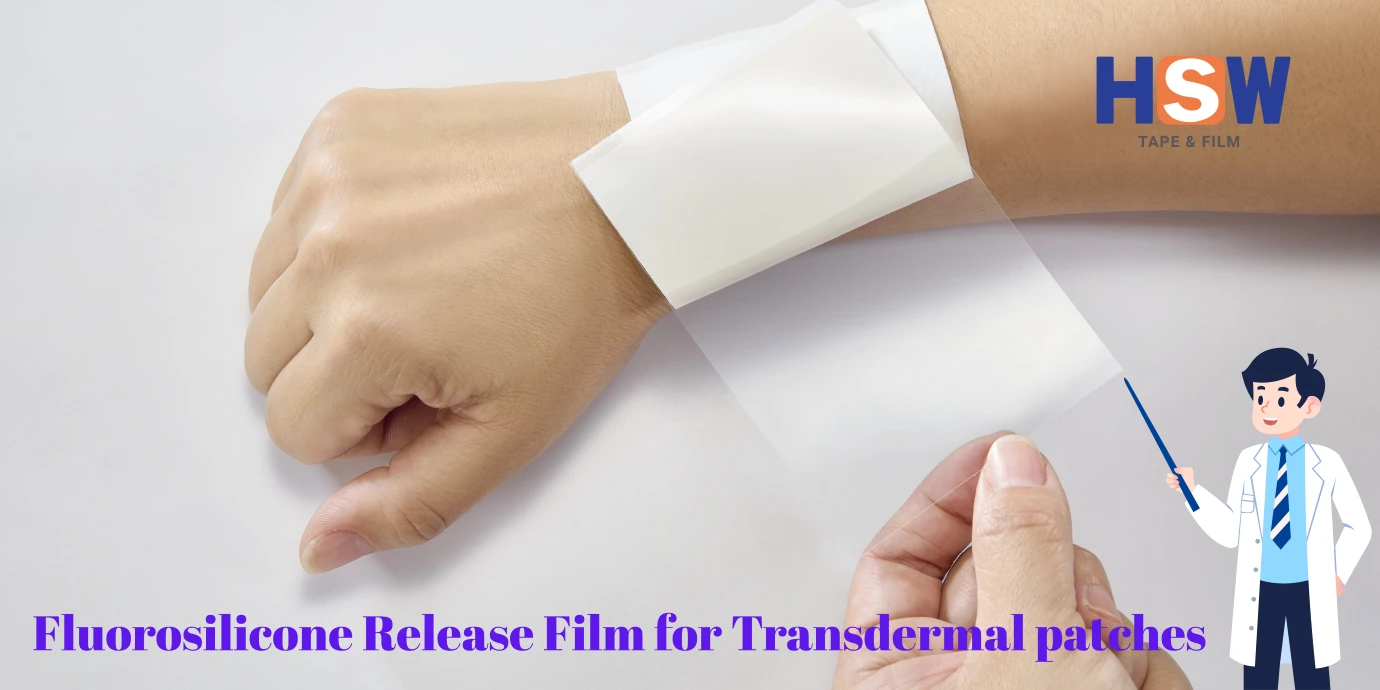
The technology principles of the release film
Introduction
Release film (also known as release liner) is a material that provides temporary protection for adhesive products and has been widely used in various aspects of our daily lives, often without being noticed. For example, the thin film peeled off before applying a bandage or medical tape is a release film. Despite its unassuming appearance, release film plays a critical "behind-the-scenes" role in modern industrial and medical products—from smartphone screen manufacturing and lithium battery packaging to food labels and medical product packaging.
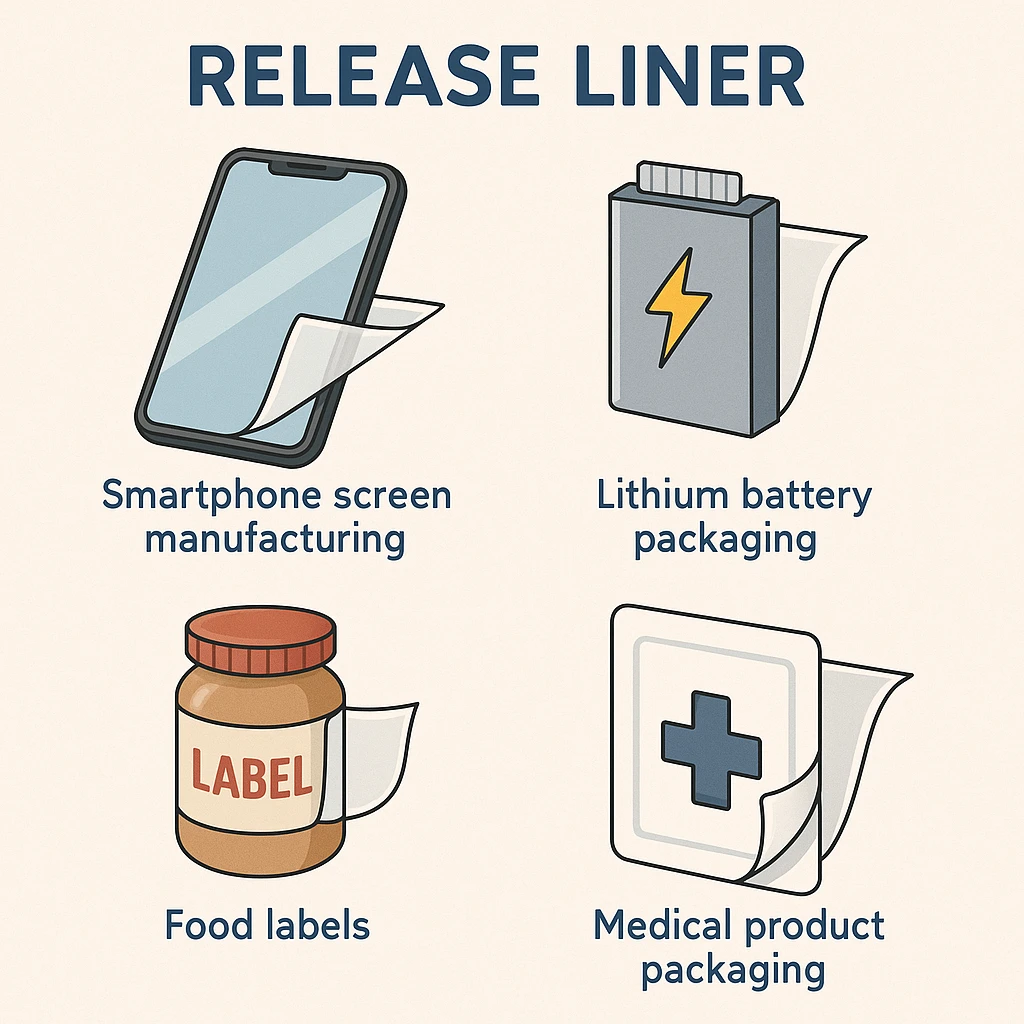
The significance of release film lies in its ability to protect the adhesive layer before use, preventing premature loss of adhesion or contamination, while ensuring easy removal during application. This improves both the convenience and safety of medical procedures. In recent years, with the rapid advancement of medical devices and dressing technologies, the demand for release film in the medical field has continued to grow. For example, the increasing prevalence of chronic diseases has driven the demand for transdermal patches and advanced wound dressings. Hospitals are also relying more on various types of adhesive sensors and conductive electrodes, all of which require high-performance release film support.
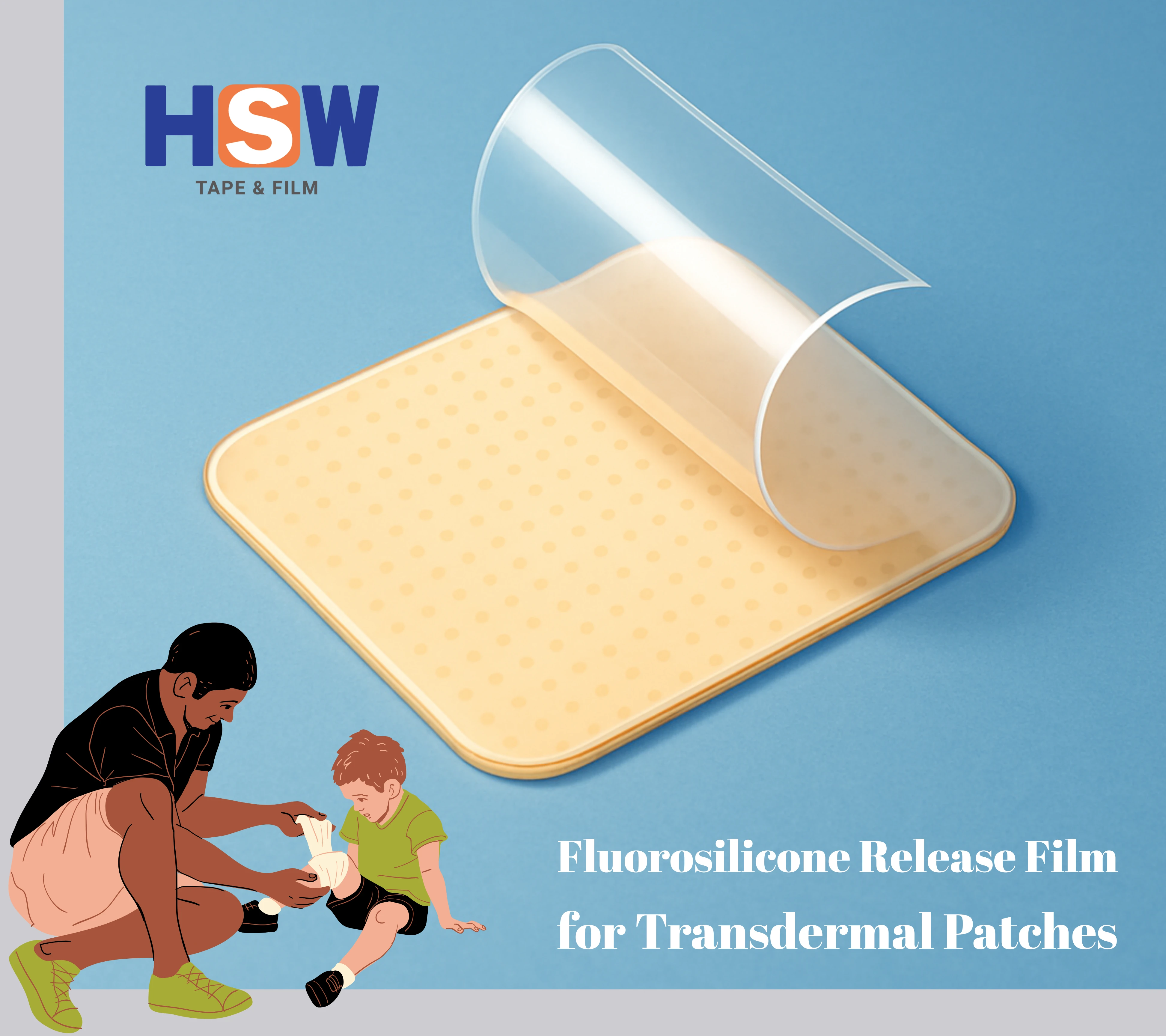
Technical Principles of Release Film
A release film generally consists of two components: the base material and the release coating.
The base material can be a specific type of paper or plastic film.
Common plastic substrates include:
- Polyester film (PET)
- Polypropylene (PP)
High-Density/Low-Density Polyethylene (HDPE/LDPE)
These materials provide the release film with good mechanical strength and stability.
The formulation and coating weight of the release layer determine the final release force and its consistency. Typically, a standard medical release film should maintain stable peel strength under most pressure-sensitive adhesives (PSAs), and can be customized to have a release force ranging from very low (e.g., 5 g/in) to relatively high (approximately 200 g/in), depending on application needs.
By adjusting the cross-linking density and thickness of the silicone coating, the required peel force can be tuned—small enough to ensure easy removal, yet not too low to risk accidental detachment during transportation.
Most release films use silicone (organosilicon) as the release coating. Silicone forms a hydrophobic, low-surface-energy network upon curing, which is suitable for various pressure-sensitive adhesives. For commonly used acrylic and synthetic rubber-based adhesives, silicone coatings can offer excellent release properties.
Depending on the practical application, release films can be designed to offer different levels of peel strength, such as light-release, medium-release, or heavy-release.
- Light-release films require only minimal force to peel off, and are typically used with soft adhesives or in applications sensitive to the peeling process (e.g., drug-infused patches where the adhesive layer must remain intact).
- Heavy-release films, by contrast, require higher force to remove, and are used in situations where secure adhesion during transport and storage is critical—such as small, heavy patches that require stronger release force to stay in place.
The level of release force is usually measured through standard peel tests, with units expressed in grams per inch (g/in) or grams per 25 mm (g/25 mm). For instance, some medical-grade release films are classified as "easy-release" if they have a typical peel force below 50 g/in (around 50 g/25 mm), which is sufficient to meet the needs of most medical pressure-sensitive adhesive applications.